Alkuviikosta Euroopan avaruusjärjestö ESA julkisti AMAZE-projektin, jonka tavoitteena on kehittää metallien 3D-tulostuksesta monipuolinen teollisuudenala. Lontoon Tiedemuseossa pidetyn tiedotustilaisuuden otsikko oli perinteiseen tapaan tulostettu, mutta vähemmän perinteiseen tapaan tuloste oli kolmiulotteinen metalliverkko. Uudella tekniikalla on mahdollista valmistaa melkein minkämuotoisia ja -kokoisia kappaleita tahansa – aikaa, energiaa ja materiaaleja säästäen. 3D-tulostuksesta kerrotaan enemmän täällä ja etenkin sen avaruussovelluksista täällä.
Euroopan avaruusjärjestön teknologinen keskus ESTEC (European Space Technology and Research Centre) on noin 3000 ihmisen työpaikka Atlantin rannalla Noordwijkissa, Hollannissa, runsaan puolen tunnin ajomatkan päässä Amsterdamista lounaaseen.
ESTECissä koordinoidaan pääosa Euroopan avaruusjärjestön teknillisistä toiminnoista, joten sijainti keskellä Eurooppaa hyvien liikenneyhteyksien varrella on mitä sopivin keskuksen toiminnalle.
Sen rooli euroopalaisessa avaruusohjelmassa on ollut vaikuttava, sillä käytännössä kaikki ESAn avaruuteen laukaisemat luotaimet ja satelliitit ovat joko kulkeneet ESTECin kautta tai niiden tekemistä tai testaamista on valvottu sieltä.
Hyvin kansainvälisessä ESTECissä on edustettuna useita kymmeniä eri kansallisuuksia, ja heidän joukossaan on tällä haavaa 17 suomalaista. Itse siirryin avaruuspuolelle suomalaisen ilmailun parista 15 vuotta sitten monen sattuman summana, joskin ESTECin ja kansainvälisen avaruustoiminnan tavat olivat osin jo tuttuja aikaisempien ESAn hankkeisiin liittyneiden työtehtävien kautta.
Vaikka ESTEC oli siten periaatteessa tuttu, oli sen erilaisten toimintojen määrä aluksi kuitenkin suuri hämmästys. Keskuksen alueella on toimistoja ja teknillistä infrastruktuuria, missä kehitetään, toteutetaan ja verifioidaan projekteja yksinkertaisista, keveistä koesatelliiteista kunnianhimoisiin, kauas avaruuteen lentäviin luotaimiin.
Monipuolista työtä monikansallisessa ympäristössä
Sulautumiseni monikansalliseen ilmapiiriin tapahtui nopeasti. Kansallisuudet häviävät isojen teknologiahaasteiden kanssa työskennellessä; nyt divisioonassani työskentelee yli kymmenestä eri maasta olevia henkilöitä.
Päivittäiset rutiinini sisältävät varmasti samoja asioita kuin vastaavan tason tehtävät muualla teollisuudessa: on teknisiä ongelmia, projektien aikatauluttamista ja resursointia, henkilöstöhallintoa ja strategiatyötä. Vain konteksti on hieman eksoottisempi, sillä yhden päivän aikana saatan olla palavereissa, joissa aiheina ovat esimerkiksi Merkuriuksen luokse lentävän BebiColombo-luotaimen lämmönkesto tai jo laukaisualustalla Ranskan Guayanassa seisovan ATV-kuljetusaluksen sisäilman laatu.
Matkustaminen on olennainen osa työtä, sillä ajastani noin 70% kuluu operatiivisten toimien parissa. Kun kyseessä ovat hyvin usein isot budjetit ja niiden aikataulut, on silloin parasta kohdata teollisuuden edustajat heidän kotikentällään. On tärkeää nähdä konkreettisesti teknologia, jonka parissa työskennellään, ja tavata samalla henkilökohtaisesti koko teollinen tiimi insinööreistä resursseista vastaavaan johtajaan. Tehtävät millä tahansa tasolla Euroopan avaruusjärjestössä mielenkiintoisen näköalapaikan Euroopan avaruusteollisuuteen, sillä olemme mukana monessa!
Tämän voi nähdä konkreettisesti esimerkiksi ESTECin sydämessä, sen testauskeskuksessa, missä avaruuslaitteita koetellaan avaruuden ja laukaisun simuloiduissa olosuhteissa. Näin halutaan varmistaa se, että ne toimivat oikeasti myös avaruudessa; parhaimmassakin monimutkaisessa laitteistossa on aina joitain suunnitteluvirheitä, ja ne on parempi löytää ennen laukaisua testauksessa kuin vasta avaruudessa. Mikäli satelliitista tai luotaimesta ei ESTECin grillauksessa ja täristämisessä löydy mitään pientäkään, on syytä olla huolissaan.
Juuri parhaillaan ESTECin halleissa on Galileo-navigointijarjestelmän ensimmäisiä tuotantosatellitteja sekä Bepi-Colombo -luotaimen insinöörimallit. Galileo-systeemin ensimmäiset satelliitit ovat jo taivaalla, mutta nämä ensimmäiset poikkeavat hieman tästä eteenpäin lähetettävistä satelliiteista, joita tehdään kolmisenkymmentä kappaletta sarjatuotantona. Nämä muodostavat itse navigointijärjestelmän satelliittiverkoston. BepiColombon insinöörimalli on puolestaan täsmälleen samanlainen kuin lopullinen, huimalle matkalle kohti aurinkokunnan sisintä planeettaa lähtevä luotain. Mallilla varmistetaan se, että laitteistot toimivat kuten on aiottu; nykyisin tietokonesimulaatioilla voidaan "koekäyttää" luotaimia jo erinomaisesti, mutta niillä ei voi korvata vielä oikean mallikappaleen tekemistä ja sen oikeissa olosuhteissa tapahtuvaa testaamista.
ESTECin kautta ovat kulkeneet myös parhaillaan joulukuussa tapahtuvaa laukaisuaan odottava GAIA ja juuri kiertoradalle lähetetty Maan magneettikenttää mittaava SWARM-satelliittikolmikko.
Suomalaisia on mukana kaikissa edeltävissä hankkeissa ja muut ESTECin suomalaiset ovat moninaisissa tehtävissä hallinnosta terveyspalveluiden kautta tieteeseen ja tekniikkaan. Siis myös muut kuin avaruusalan henkilöt voivat päätyä ESTECiin.
Omaa tehtäväni materiaali- ja komponenttidivisioonan johtajana on varmistaa, että avaruusmateriaaleihin ja sähköisiin komponentteihin liittyvä laatu on riittävää ja että alan teknologiakehitystä viedään ESAn tulevien tarpeiden mukaan eteenpäin. Avaruuslaitteita kehitettäessä katseen pitää olla pitkällä tulevaisuudessa, sillä teknologiat, joita kehitämme tänään, saattavat olla laukaisualustalla vasta vuosikymmenen päästä. Siksi teemme työtä laajasti ja käytämme hyväksi jokaisen jäsenmaan korkeakoulujen ja instituuttien parhaita resursseja.
Kuuminta hottia juuri nyt: 3D-tulostus
Viime aikoina suurimmat otsikot perusteknologioiden on saanut 3D-tulostus, mitä ESAssa on tutkittu ja kehitetty jo vuosikymmenen ajan. Nyt tekniikka on tulossa myös yleisempään käyttöön, mutta erityisesti avaruusalalla se tarjoaa uskomattomia mahdollisuuksia. Uskon, että se on merkittävä tekijä myös rakentaessamme tulevaisuuden avaruusalusarkkitehtuuria. 3D-tulostus tekee mahdolliseksi nopean tuotekehityksen suunnitelmasta lopputuotteeseen ja sen avulla voidaan tehdä uusia optimoituja geometrioita, jotka vähentävät merkittävästi painoa ja aina ongelmia tuottavia materiaaliliitoksia.
Esimerkiksi kuvassa oleva Kansainvälisellä avaruusasemalla käytettävä vesiventtiili on 3D-tulostettuna 40% kevyempi kuin perinteisellä tavalla valmistettu; keskimmäinen on alkuperäinen, vasemmalla samanlaisesta metallista tulostettu ja oikealla titaanista tulostettu optimoitu kevytversio. Olennaisin eroavaisuus on keskimmäisessä oleva hitsaussauma, mitä tulostetuissa ei ole.
Tavoitteenamme ei ole pelkästään toistaa 3D-tulostimella osia, joita tehdään tällä hetkellä muilla valmistusmenetelmillä, vaan pyrimme integroimaan koko suunnittelu- ja valmistusketjun palvelemaan uutta teknologiaa. Tällöin saavutamme täysin optimoidun, funktionaalisia vaatimuksia vastaavan lopputuotteen, jonka ominaisuuksia eivät enää rajoita perinteisten valmistusmenetelmien reunaehdot.
Suunnittelun, valmistuksen ja laadunvalvonnan rajojen rikkominen mahdollistaa uuden suoritusarvotason. Ajatelkaapa vaikkapa auton moottoria, jonka suunnittelua ja valistusta eivät rajoita esimerkiksi standardimitoitetut putket, liittimet tai pultit. Ei olekaan ihme, että keskustelemme tallakin hetkellä erään tunnetun F1-tallin kanssa teknologisesta yhteistyöstä. Avaruustekniikkaa on jo nyt kilparadoilla, mutta pian sitä on vielä enemmän!
Kaikkein parasta 3D-tulostamisessa on se, että se on ympäristöystävällistä, koska siinä ainetta ei poisteta (kuten esimerkiksi alumiinia jyrsittäessä lopulliseen muotoonsa) vaan tulosteessa käytetään vain kappaleessa tarvittava määrä ainetta. Siten valmistusprosessin tuottaman jätteen määrä saadaan minimoitua.
ESA vei mukanaan
Kun aikanaan tulin ESTECiin, kuvittelin viipyväni vain parin vuoden ajan tarkoin määritellyissä tehtävissä. Mutta toisin kävi, ja ulkomaankeikka on muuttunut pysyväksi asumiseksi Alankomaissa. Kiinnostavat teknologiahaasteet ja kansainvälinen työilmapiiri vie mennessään – niin kävi minulle, ja niin on käynyt jo monille muille suomalaisille (ja muillekin) kollegoilleni!
Mikko Nikulainen
ESAn teknologiakeskuksen ESTECin materiaali- ja komponenttidivisioonan johtaja

Printterillä avaruuteen
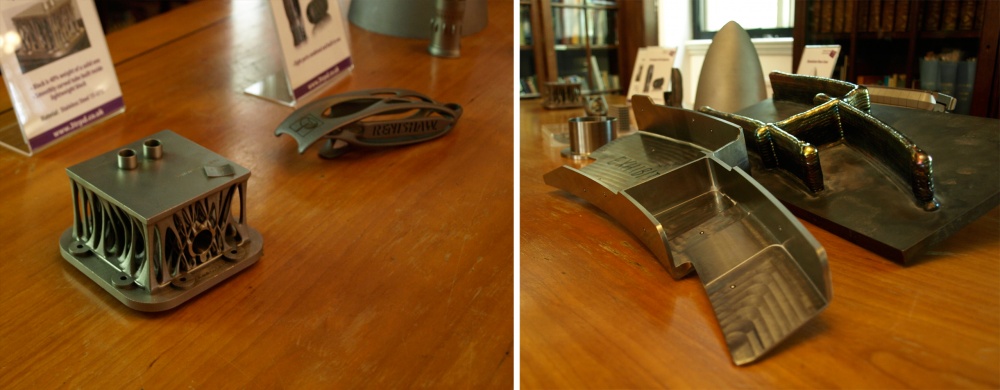
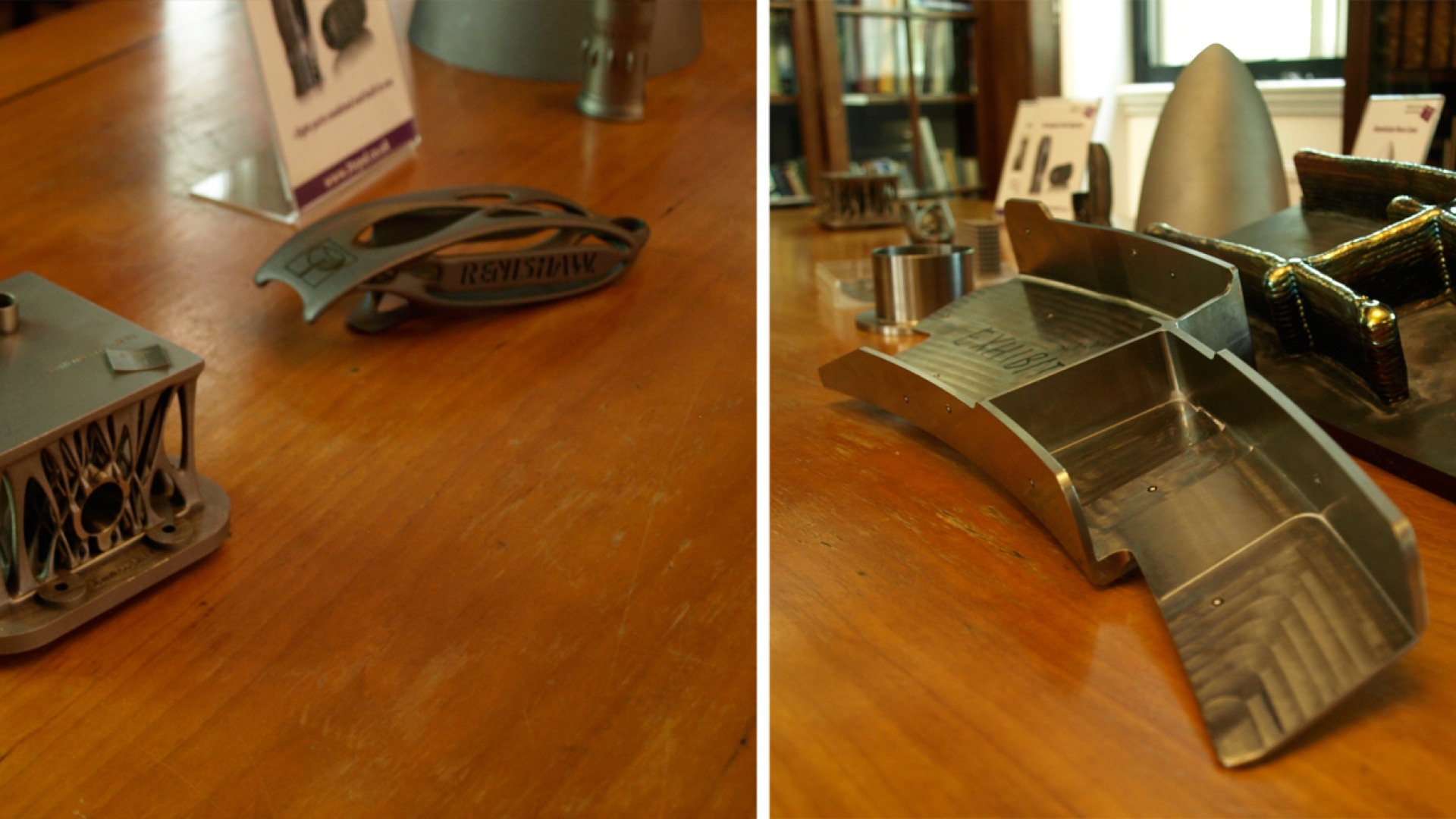
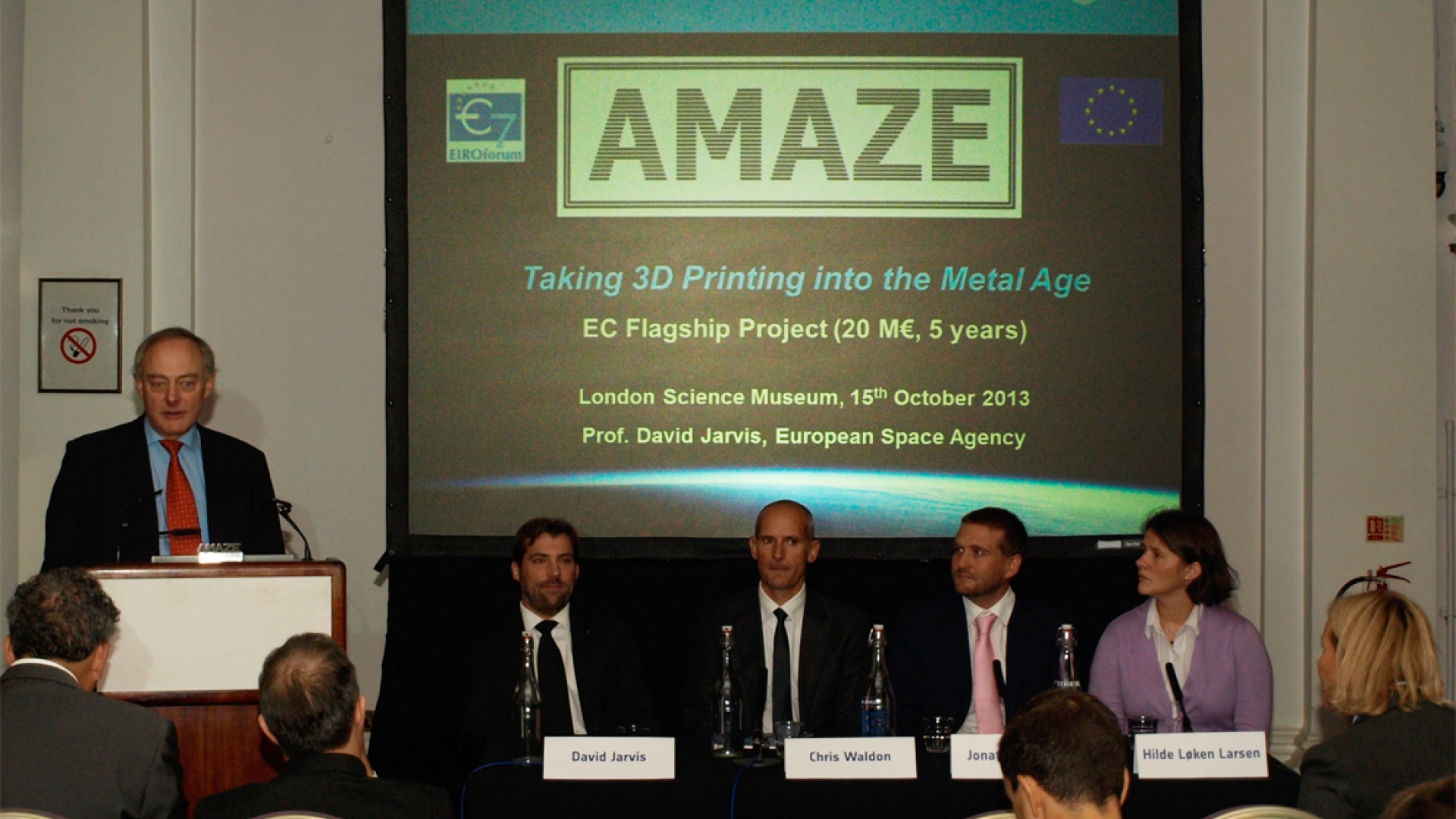
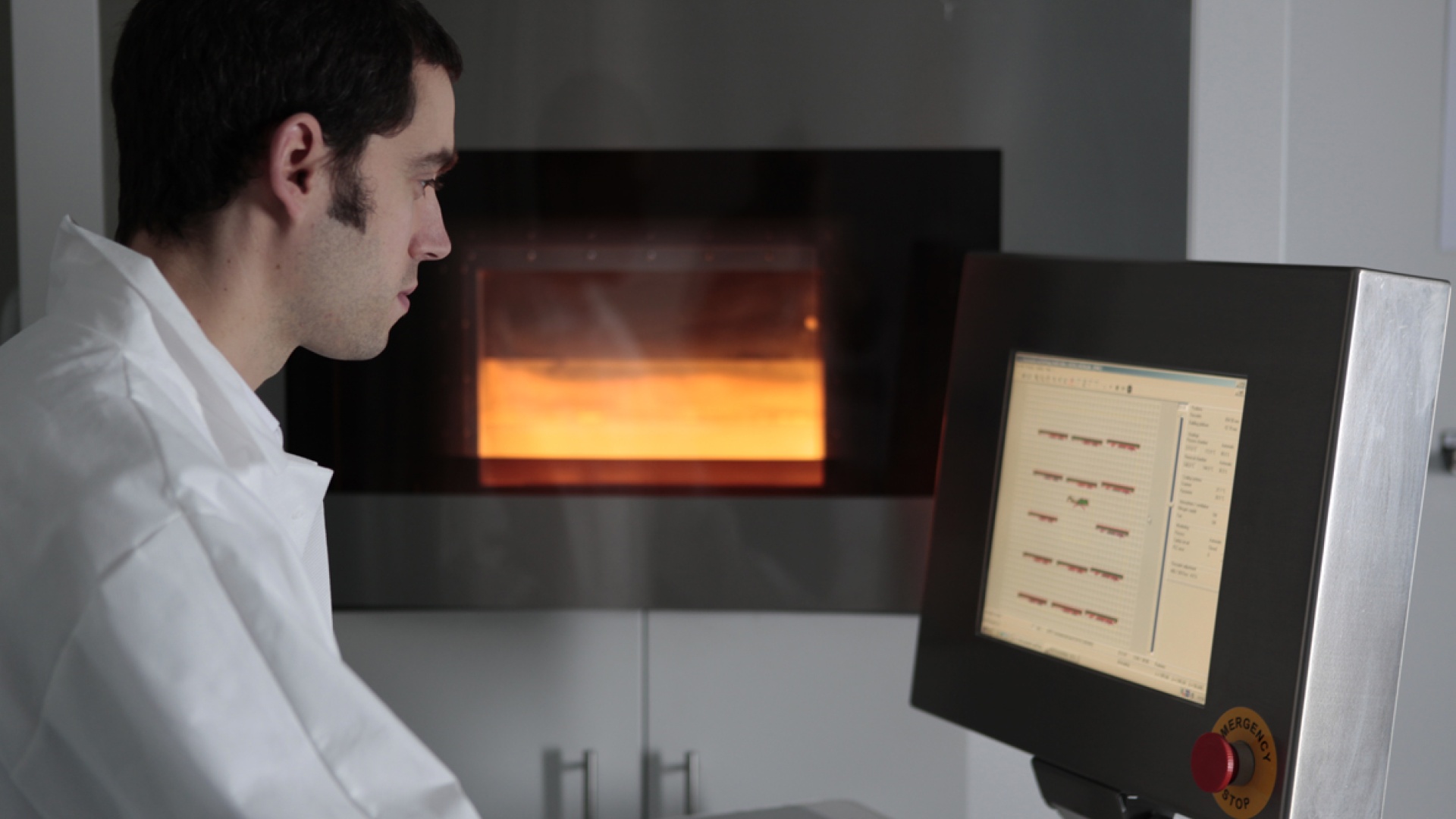
Ei nyt aivan, mutta melkein. Euroopan avaruusjärjestö ESA järjesti 15. lokakuuta Lontoon Tiedemuseossa tiedotustilaisuuden, jossa julkistettiin AMAZE-projekti (Additive Manufacturing Aiming Towards Zero Waste & Efficient Production of High-Tech Metal Products). Sen vaatimattomana tavoitteena on viedä 3D-tulostus ”metalliaikaan”.
Tilaisuuden avanneen ESAn avaruustekniikkakeskuksen ESTECin johtajan Franco Ongaron mukaan uuden menetelmän keskeisiä etuja ovat komponenttien lujuus ja keveys, materiaalihävikin merkittävä väheneminen ja ylipäätään avaruusteollisuuden ”vihertyminen”: materiaalien lisäksi 3D-tulostus säästää energiaa.
Paikalla oli edustajia useista alan yrityksistä ja tutkimuskeskuksista. Vaikka kyseessä on ESAn ”lippulaivahanke”, tarkoitus ei ole kehittää teknologiaa pelkästään avaruustutkimuksen tarpeisiin. Esimerkiksi Chris Waldon Ison-Britannian atomienergiajärjestöstä esitteli ITER-fuusiokoereaktoria, jota rakennetaan parhaillaan Ranskan Cadaracheen. Kuumuuden ja kestävyyden kannalta kriittisiä reaktorikammion osia valmistetaan 3D-tulostusmenetelmällä.

Avaruus- ja lentokoneteollisuus ovat kuitenkin merkittävässä osassa kehitettäessä uutta tekniikkaa. Kumpainenkin käyttää komponentteja, joiden laatuvaatimukset ovat äärimmäisen tiukkoja. Samalla niiden on oltava mahdollisimman keveitä, sillä etenkin avaruusrakenteissa mutta toki myös lentokoneissa kaikki ylimääräinen paino on saatava karsittua.
Perinteisillä valu- ja työstömenetelmillä on usein pakko turvautua suoriin kulmiin ja krouveihin rakenteisiin, jotta vaatimukset lujuuden suhteen saavutetaan. 3D-tulostuksella komponenteista pystytään tekemään sulavalinjaisempia, tietyllä tavalla ”orgaanisia”: valmistusmetodi ei enää sanele muotoa, vaan komponentin käyttötarkoitus ja sille asetetut vaatimukset.
Additive Manufacturing eli ”kerrosvalmistus” toimii nimensä mukaisesti. CAD-ohjelmalla suunniteltu komponentti tulostetaan tietokoneen ohjaamalla laitteistolla, joka kasaa sen kerros kerrokselta. Näin pystytään valmistamaan esimerkiksi monimutkaisia, mutta keveitä verkkorakenteita, jollaisesta on esimerkki huomisessa päivän kuvassa.
Tulostuksen jäljiltä komponentti on muodoiltaan ja mitoiltaan jo hyvin lähellä lopullista, joten työstövaihe on yksinkertaisempi ja nopeampi, ja siinä syntyvä materiaalihukka on vain murto-osa perinteisen menetelmän hävikistä. Isokokoisiakin komponentteja pystytään valmistamaan yhden vuorokauden kuluessa ja tulostettavien komponenttien kokoskaala on suuri, millimetreistä metreihin – ainakin piakkoin.
3D-tulostusta kehitetään jo kovaa vauhtia eri puolilla maailmaa, mutta ESAn tavoitteena on lisätä hankkeensa avulla yhteistyötä ja kehittää laajamittaista tuotantoa. Avaruustutkimusta on aina moitittu kalleudesta ja jopa vähäisistä hyödyistä suhteessa siihen uhrattuihin rahasummiin – vaikka monet nykypäivän arkisilta tuntuvista asioista olisivat mahdottomia ilman avaruustekniikkaa.
AMAZE-hankkeen myötä tyyriiksi arvosteltu avaruusala on tavallaan maksamassa ”velkaansa” takaisin: avaruustekniikassa sovellettavaa 3D-tulostustekniikkaa kehittämällä pystytään parantamaan myös tavallisessa teollisuudessa käytettäviä menetelmiä. Jotkut puhuvat jopa ”kolmannesta teollisesta vallankumouksesta”.
Hilde Løken Larsen, Norsk Titanium AS -yrityksen tutkimus- ja kehitystoiminnan johtaja, näkee AMAZE-hankkeeseen osallistumisen luontevana osana Norjan avaruustoimintaa, vaikka projektilla on muitakin tavoitteita kuin tulostaa avaruusalusten osia. Larsenin mukaan avaruustekniikka on kuitenkin viemässä teollisuudenalaa voimakkaasti eteenpäin.
Larsenin edustama Norsk Titanium keskittyy nimensä mukaisesti titaanikomponenttien valmistukseen. Titaani on kevyttä ja lujaa, joten sitä on perinteisesti käytetty lentokoneiden ja avaruusalusten rakenteissa. Sen sulamispiste on liki 1700 celsiusastetta, mutta Larsenin esittelemässä tulostusmenetelmässä titaanin, alumiinin ja vanadiinin seoksesta valmistetun metallilangan sulattamiseen käytetään ionisoidun argonin muodostamaa plasmakaarta, jonka lämpötila on yli 5000 celsiusastetta.
”Tällä hetkellä kehitystyö kohdistuu erityisesti komponenttien rakenteelliseen laatuun. Kun osat tulostetaan kerros kerrokselta, niiden väliin ei saa jäädä vähäisimpiäkään saumoja tai huokoisuutta. Se on aikamoinen haaste, mutta olemme päässeet jo hyvin tuloksiin”, Larsen toteaa.

Omasta innostuksestaan huolimatta EADS Innovation Worksissa tutkimusryhmää johtava Jonathan Meyer toppuuttelee vielä innokkaampia: ”Joidenkin mielestä 3D-tulostus on ratkaisu kaikkeen. Ei se kuitenkaan ole. Sillä pystytään valmistamaan monia sellaisia komponentteja, joiden valmistus perinteisin valu- ja työstömenetelmin on hyvin hankalaa ja kallista tai tyystin mahdotonta, mutta silläkin on rajoituksensa. Hassua kyllä, yksinkertaiset asiat ovat hankalimpia. Yksi hyvä esimerkki ovat umpimetalliset, massiiviset kappaleet. Sellaisia ei kannata valmistaa 3D-tulostuksella, koska niihin muodostuu voimakkaita jännityksiä.”
Tieteiskirjallisuuden kuvitelmat ovat silti muuttumassa vähitellen todellisuudeksi, kun metallijauheesta tai -langasta voidaan tulostaa melkein minkämuotoisia kappaleita tahansa. Ja kohta myös missä tahansa: Kansainväliselle avaruusasemalle ollaan viemässä ensi vuonna 3D-tulostinta. Tosin Meyer on siinäkin suhteessa sanoissaan varovainen: ”Pikapuoliin science fiction voi olla todellisuutta, mutta ei ihan vielä.”
Aiheeseen liittyy Lontoon Tiedemuseossa vastikään avattu näyttely 3D: printing the future, joka on avoinna ensi kesään saakka. Lisätietoja löytyy Tiedemuseon sivuilta.
3D-tulostuksen avaruussovelluksista on kerrottu tarkemmin Tiedetuubin ESA-blogissa.
3D-tulostus mullistaa avaruuttakin

Euroopan avaruustekniikkakeskuksen ESTECin käytävälle oli ilmestynyt omituinen betonikappale. Erilaisten avaruuslaitteiden ja satelliittimallien, joita avaruuskeskuksen seinillä ja käytäville on aseteltu ihmeteltäväksi, keskellä on nyt möhkäle betonia – siinä aivan Hubblen aurinkopaneelin vieressä.
Kyse ei kuitenkaan ole mistä tahansa palasesta betonia, vaan puolitoista tonnia painava mallikappale mahdollisen kuuaseman rakennusmateriaalista, joka on tehty Kuun pinta-ainetta muistuttavasta seoksesta 3D-tulostusmenetelmällä.
Juuri tästä kappaleesta ja sen tekemiseen käytetystä tekniikasta kerrottiin viime keväänä, kun ESA julkaisi tutkimuksen uudesta tavasta tehdä kuuasema aikaisempaa kätevämmin ja edullisemmin. Ryhmä rakennus- ja avaruusalojen asiantuntijoita, muun muassa tunnettu arkkitehtiyhtiö Foster + Partners, olivat lähestyneen aseman rakentamisen ongelmaa aivan uudesta näkökulmasta: ei mitään esivalmistettuja sylintereitä, jotka laukaistaisiin ensin kiertoradalle, hilattaisiin sieltä Kuun ympärille ja laitettaisiin laskeutumaan sen pinnalle, vaan koko asema voitaisiin tehdä paikan päällä, paikallisista materiaaleista.
Kätevin tapa valmistaa rakennuspalasia on käyttää sovellettua 3D-tulostintekniikkaa. Erikoisprintterin lähettäminen olisi suhteellisen edullista, ja sillä voitaisiin tehdä juuri sellaisia osia, mitä tarvitaan. Kun eri muotoisten, sisäosiltaankin monimuotoisten osien tekeminen olisi mahdollista, voitiin aseman suunnittelussakin ottaa uusia vapauksia.
Tuloksena oli kupolirakenne, joka haudataan Kuun pinnan alle. Sen "tiilet" olisivat lintujen luiden tapaan sisältä osittain onttoja, ohuiden, tarkasti laskettujen ja sijoiteltujen tukiranteiden täyttämää tyhjää tilaa, jolloin kappaleet olisivat lujia sekä kestäviä, mutta myös kevyitä ja niiden tekeminen vaatii vähän ainetta. Paitsi että muoto voitaisiin tehdä aivan millaiseksi halutaan, myös sisältä, olisi materiaalihävikki minimaalinen.
Brittiyhtiö Monolite onnistui valmistamaan juuri halutunlaisia rakennuspalasia D-Shape -tulostimellaan, joka on suunniteltu jopa kuusi metriä halkaisijaltaan olevien maanpäällisten rakennuskappaleiden valmistamiseen. Se tuottaa hiekkamaisesta raaka-aineesta betonia sekoittamalla siihen sidosainetta ja ruiskuttamalla aineen pienempien 3D-tulostinten tapaan kerros kerrokselta haluttuihin kohtiin tietokoneen ohjaamana.
Itse asiassa jättibetoniprintteriä on käytetty rakennusten sijaan toistaiseksi eniten keinotekoisten koralliriuttojen ja taideteosten tulostamiseen.
Kuun tapauksessa betoni olisi kuun pintaregoliittia, mihin lisätään ensin magnesiumoksidia ja tulostettaessa suolaa, mikä muuttaa aineen kivenkovaksi. Laitteella voisi tulostaa yhden kuuaseman periaatteessa viikossa. Huimaa!
Avaruus tuo uutta maanpäälliseenkin 3D-tulostukseen
Samalla kun kolmiulotteinen tulostus leviää Maan päällä, ollaan myös avaruusasemalle lähettämässä 3D-printteriä.
Se, että monien yksittäisten varaosien asemalle rahtaamisen sijaan osia voitaisiin tulostaa muovi- tai metalliseoksista siellä tarpeen mukaan on huima askel eteenpäin. Ongelmana avaruudessa on tosin painottomuus, mutta siihenkin on omat ratkaisunsa. Tulevaisuudessa, kun lennetään kauemmaksi ja kaikkien mahdollisten osien pakkaaminen mukaan on hankalaa, on printteri todella suureksi avuksi.
3D-tulostuksen vääntäminen avaruuskelpoiseksi on kehittänyt tekniikkaa myös maanpäällisessä käytössä paremmaksi. Varsin voimakasta tämä kehitys on ollut Euroopan avaruusjärjestön teknologiaosastolla, missä on kehitetty aivan uusi, mullistava tapa tehdä metallisia, hyvin vaikeita olosuhteita kestäviä 3D-tulosteita. Hanke on osoittautunut niin kiinnostavaksi kaupallisesti, että sen ympärille on kerätty ESAn, Euroopan unionin ja alan teollisuusyritysten yhteinen AMAZE-projekti.
Tätä monessa mielessä vallankumouksellista tekniikkaa esitellään Lontoon Tiedemuseossa nyt lokakuun 15. päivänä ja Tiedetuubissa kerrotaan luonnollisesti heti päivän annista.
Myös muut tiedotusvälineet ovat tervetulleita tilaisuuteen: kutsu sinne on ESAn nettisivuilla.
Tulosta hammasharjasi ja harjaa nopeammin
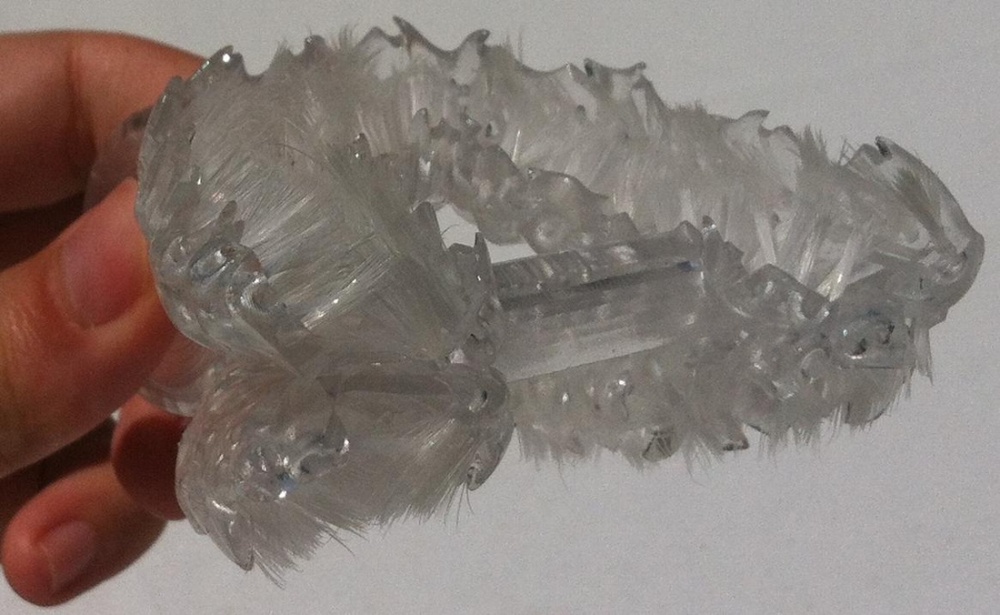
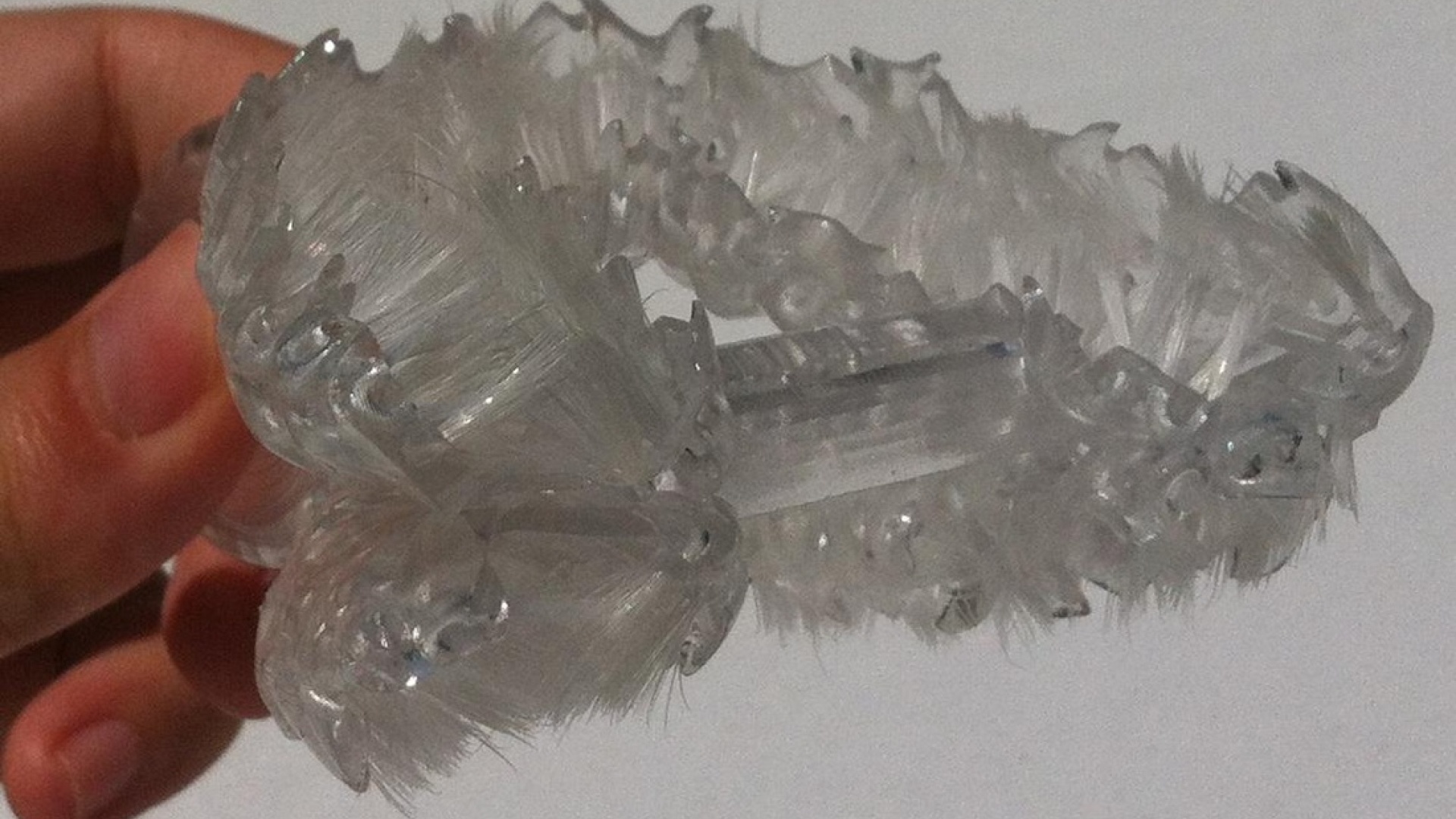
.
Jos sinulla on jo sähköhammasharja, kenties haluat pian siirtyä takaisin harjaamiseen: tämä hammasharja on nimittäin kaikkea muuta kuin perinteinen.
Blizzident on 3D-tulostettu henkilökohtainen hammasharja, joka on suunniteltu sopimaan vain käyttäjälleen. Hammaslääkärin luona voi teettää ensin suustaan ja hampaistostaan 3D-skannauksen, joka ladataan harjaa tekevän yhtiön nettisivuille. Yhtiö valmistaa sen perusteella "käänteisen" muovikappaleen suun sisäosistasi ja kiinnittää siihen hyvin ohuita harjaksia.
Tällä harjalla ei harjata klassiseen tapaan, vaan se laitetaan suuhun ja sen jälkeen hampaita vain hangataan toisiaan vasten samaan tapaan kuin paikkauksen jälkeen hammaslääkärissä etsitään väripaperin avulla uuden paikan oikeaa muotoa. Yhtiön mukaan vain 15 oikeanlaista hampaiden jauhamisliikettä riittää puhdistamaan hampaat ja niiden välit tehokkaasti.
Hammastahnaa ei tässä levitetä harjaan, vaan kielen päälle. Siitä kielellä sitä nostetaan ylähampaiden pinnalle ja hampaita toisiinsa ilman harjaa hieroen tahnaa siirtyy sopivasti myös alahampaille. Harja puhdistaa samalla myös kielen.
Paremman lopputuloksen lisäksi aikaa säästyy. 3D-harjaukseen kuluu kuuleman mukaan vain kuusi sekuntia, missä on roima ajansäästö perinteiseen harjaukseen verrattuna. Blizzidentin mukaan – lukua lienee siis liioiteltu – tavallinen hammasharjaaminen vie noin 10 minuuttia päivässä, mikäli sen tekee kunnolla harjan ja hammasvälipuhdistimien kanssa, kun taas uudella tavalla tähän kuluu vain minuutti. Yhtiön matemaatikoiden mukaan tämä säästää vuodessa 3285 minuuttia, eli vuositasolla voit käyttää 55 tuntia johonkin muuhun kuin hampaiden harjaamiseen!
3D-tulostamalla tehdyllä hammasharjalla on toki omat huonot puolensa, joista suurin toistaiseksi on se, että harjan tekemiseen käytety 3D-tulostinmuovi ei ole vielä hyväksytty kaupallisesti lääketieteellisessä laitteessa käytettäväksi. Harja sinällään ei kaipaa viranomaisten hyväksyntää, mutta sen muovin turvallisuus pitää testein varmistaa.
Toinen huono puoli on hinta. Yhtiön mukaan harjan tekeminen maksaa 300 Yhdysvaltain dollaria, siis noin 220 euroa, ja suun skannaaminen täytyy tehdä hammaslääkärillä, joka laskuttaa siitä 100-150 euroa. Eivätkä kaikki hammaslääkärit toistaseksi tee skannauksia. Harjan voi hankkia toki myös lapsille, mutta lasten suu muuttuu kasvamisen myötä hyvin nopeasti, joten suu pitäisi skannata ja harja uusia useamman kerran vuodessa.
Kolmas heikko lenkki on lyhyt harjausaika: sen kuluessa hammastahnan fluori ei todennäköisesti ennätä kiinnityä tarpeeksi hampaisiin. Niinpä fluoraus pitäisi sitten tehdä uudelleen.
Jotenkin voisi ennustaa, että tästä hammasharjasta ei tule mitään suurta menestystä, mutta on jännä osoitus 3D-tekniikan mahdollisuuksista!
Alla on yhtiön mainosvideo:
Päivän kuva 20.6.2013: Superpieni 3D-printattu akku

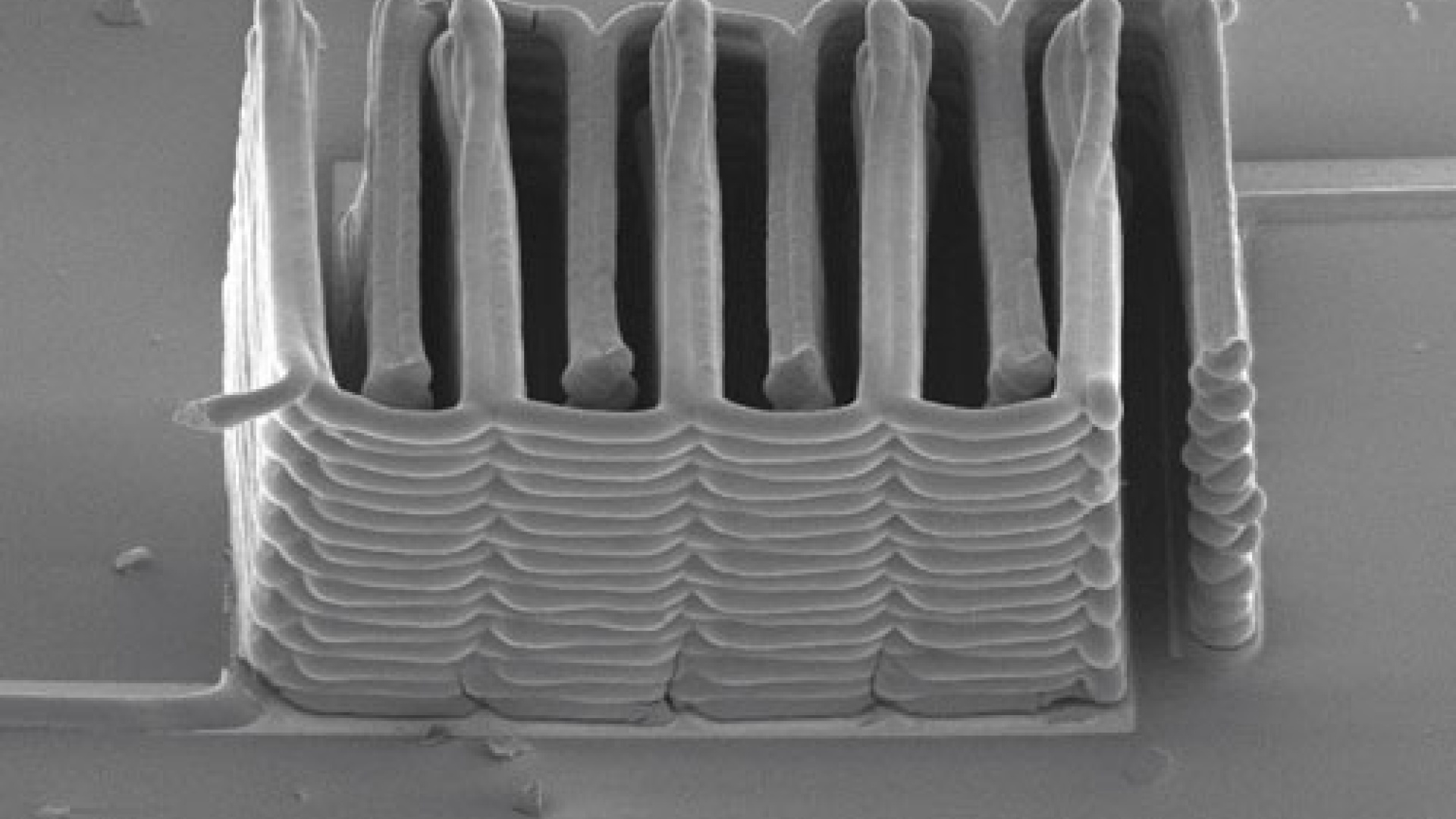
Kyllä, tämä on aivan oikea, toimiva litiumioniakku. Erikoiseksi sen tekee paitsi se, että se on valmistettu 3D-printterillä, niin myös se, että se on kooltaan hiekanjyvän luokkaa.
Harvardin yliopiston ja Illinoisin Urbana-Champaignissa olevan yliopiston yhteistutkimuksessa haluttiin löytää tekniikkaa, jolla minikokoisten akkujen tekeminen yksinkertaisesti printtaamalla olisi mahdollista. Näin akuista voitaisiin tehdä juuri halutun kokoisia ja muotoisia, sekä tarvittaessa erittäin pieniäkin.
Elektronimikroskooppikuva: Jennifer A. Lewis
Verisuonia 3D-tulostimella

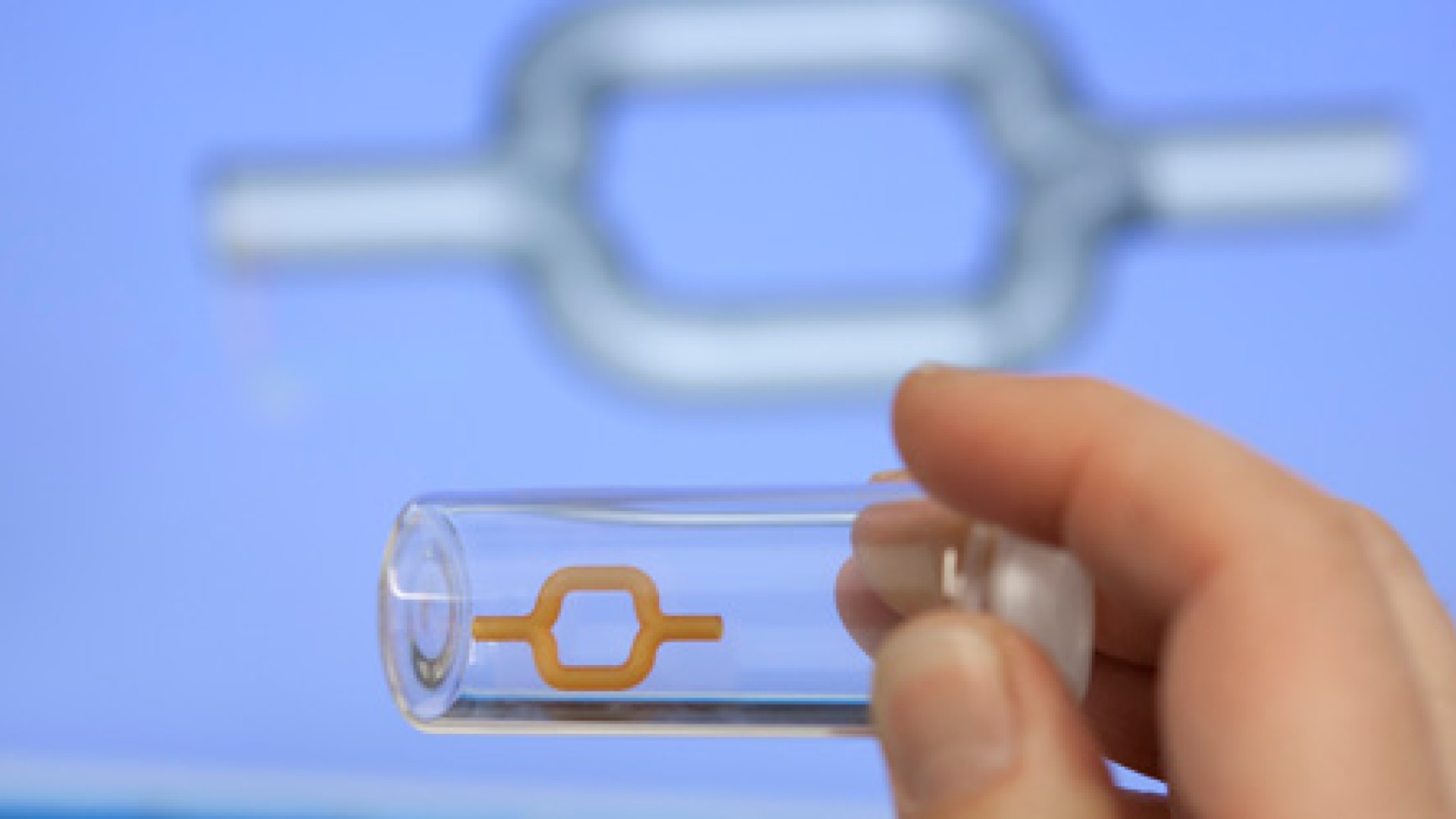

3D-tulostus kehittyy kovaa vauhtia ja siitä puhutaan – aiheestakin – joka puolella, koska sillä on suuret mahdollisuudet. Tekniikalla voi pian myös tulostaa verisuonia ja kudoksia ihmisille.
Aalto-yliopiston Kemian tekniikan korkeakoulu ja BIT-tutkimuskeskus ovat mukana tutkimuksessa, jonka tavoitteena valmistaa verisuonitettua keinoihoa 3D-tulostimilla. Ensisijaisesti keinoihoa on tarkoitus käyttää apuna farmasia- ja kosmetiikkateollisuudessa korvaamaan eläinkokeita, mutta sen avulla voidaan myös kasvattaa ihoa palovammojen ja niistä aiheutuneiden traumojen hoitoihin.
Keinokudokset koostuvat polymeereistä, ja tavoitteena on kehittää mahdollisimman lähelle ihon ominaisuuksia ja koostumusta olevia biopolymeerejä. Hankalinta on saada materiaalihin juuri halutunlaiset ominaisuudet, koska samalla niiden tulee olla nestemäisiä tai helposti nesteytyviä ja myös nopeasti kovettuvia, jotta niitä voitaisiin käyttää 3D-tulostimissa raaka-aineena. Lisäksi niistä valmistetun kudoksen on oltava elastinen ja sovelluttava elimistöön.
Aalto-yliopistossa materiaaleja koskevan työpaketin vetäjä on akatemiaprofessori Jukka Seppälä.
Tutkimuksessa on mukana myös Minna Malin biotekniikan ja kemian tekniikan laitokselta. "Kehitettävät materiaalit jaetaan kolmeen pääryhmään, joita ovat valon vaikutuksesta kovettuvat polymeerit, lämmön tai paineen avulla työstettävät termoplastit sekä hydrogeelit", kertoo Malin. "Jokaisella on oma roolinsa suunnitellussa kudosmallissa."

Aalto-yliopiston BIT-tutkimuskeskuksessa valmistetaan polymeeristä alkuperäisiä kudoksia tai verisuonia muistuttava kudosmalli 3D-tulostustekniikalla. Halkaisijaltaan sata mikrometriä olevat suonet tehdään periaatteessa yksinkertaisella mustesuihkutekniikalla ja sitä pienemmät hiussuonet korkean resoluution kaksifotonilaser-tekniikalla.
Sen jälkeen verisuonirakenne ympäröidään hydrogeelillä ja nanokuiduista muodostetulla verkkorakenteella, jotka toimivat erityyppisten solujen kasvualustoina. Hienovarainen ja vaikeasti toteuttettava versiuonirakenne on tärkeää, jotta keinoiho saa ravinteita ja voi hoitaa aineenvaihduntansa normaalin ihon tapaan.
BIT-tutkimuskeskuksessa työtä vetää keskuksen johtaja Jouni Partanen, joka on maailman johtavia 3D-tekniikoiden kehittäjiä.
Keinokudosten 3D-tulostushanke on alkanut vuonna 2011 ja sen on määrä päättyä lokakuussa 2015. Monitieteellisessä hankkeessa on mukana kaikkiaan 16 osapuolta Euroopasta. Aalto-yliopisto osallistuu yhteensä viiteen projektiin kuuluvaan työpakettiin. Aalto-yliopiston suurin rooli on uusien materiaalien kehittämisessä, karakterisoinnissa ja suonimallitiedostojen luomisessa.
Projekti kuuluu ArtiVasc 3D -nimiseen tutkimusohjelmaan, joka on osa EU:n 7. puiteohjelmaa.
Juttu perustuu Aalto-yliopiston tiedoteeseen Keinotekoisia verisuonia ja kudoksia 3D-tulostimen avulla.